Media Blast Process
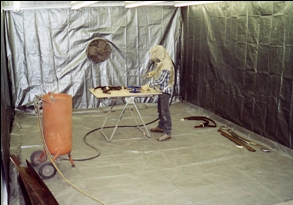
Our indoor Media Shop allows us to blast 365 days per year. When you are able to blast on any given day it helps each project to run smooth.
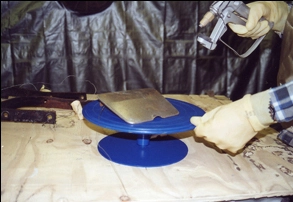
We use special tools including turn tables to make work easier which keeps the body from fatigue.
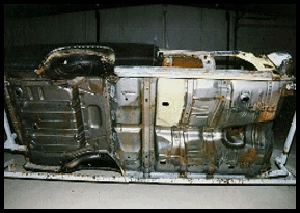
We use body and frame rotators to ensure every square inch has been done.
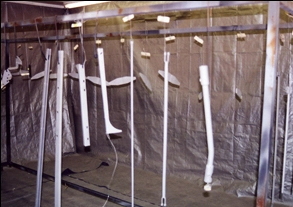
Each and every part is blasted to white metal clean and inspected , marked and touched up if needed. Before any primer is applied.
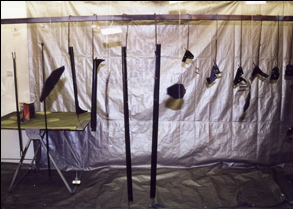
The parts are then sprayed with DP 90- epoxy by Ditzler. The ultimate adhesion and corrosion protection primer available!
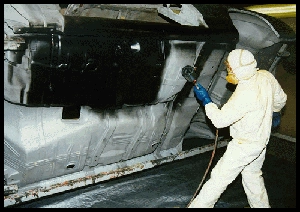
Here Steve is priming the underside of the Chevelle SS with DP-90 epoxy immediately after blasting.
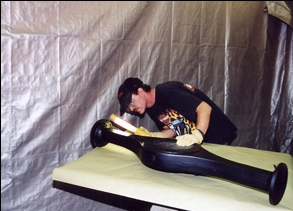
Final inspection of primed parts is also done to check for 100 % coverage.
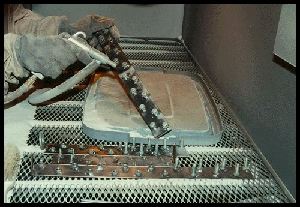
Over the years we have designed many jigs to accomplish more in less time such as bolt holders during blasting for more efficient work.
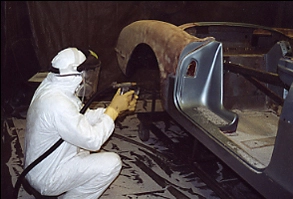
We strip paint using plastic media because of its speed and efficiency. Fiberglass cars like Corvette, Avanti, Shelby Mustangs etc are prime candidates as you must strip paint gently to avoid harming the gel coat and fiberglass strands.
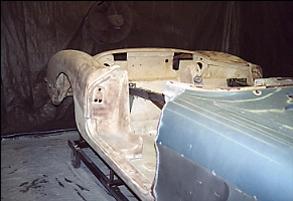
Cleaned down and ready to start repairs. The front clip on this one is heavily damaged and is beyond the cost of repair compared to the new front clip available so we will replace it .
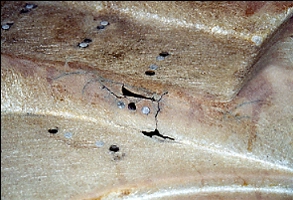
Stripping the body every square inch reveals all of the sin. As you can see the trunk had a stress point and started cracking. As time went by pieces fell out making the hole larger.
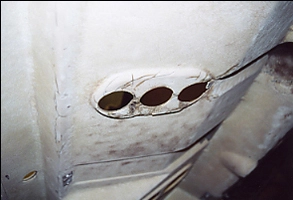
Dirt and grease can soak into the glass body around edges and any areas that the gel coat has been worn through to the fiberglass strands. If left unattended exfoliation takes place and the whole thickness of that section will have to be replaced.
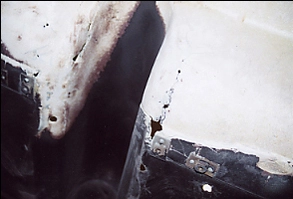
When you strip a car down to this level you will find every tiny hole and stress crack there is. As I always say " You can not fix what you can not find" Therefore we must use the techniques and tools to inspect and reveal everything.
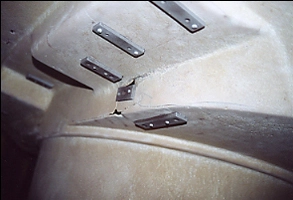
Another look shows metal reinforcements that need aluminum oxide blasting after they are removed. We will then prime them using zinc chromate and reattach them using new rivets !
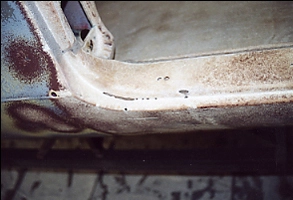
As seen even the door opening has stress cracks where epoxies were used to adhere the separate panels together to form a complete automotive body.
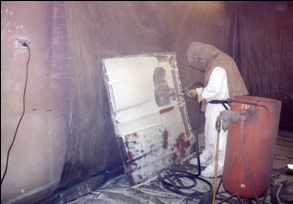
Injection molded parts can be blasted more aggressively compared to hand laid parts and bodies as with the above Corvette. Nat is stripping the paint of this Formula Firebird hood while leaving the factory gel coat untouched.