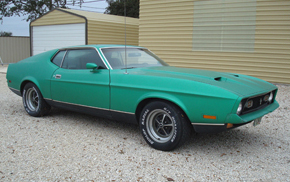
At first glance, this car appears to be a great candidate for a custom car build, but looks can be deceiving! Custom car building involves many steps, and we start off by photographing every part of the project for reference during final assembly and also to show you the true condition of your project. We usually provide 200-400 photos during the disassembly and a minimum 2000 photos of the entire build process. With all the photographs, documentation, phone call records, and original receipts proving no profit on parts it gives you peace of mind.
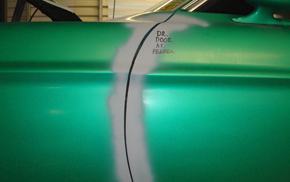
One of the first things we do with any classic car is inspect the project for body panel-to-panel flushness and how inconsistent the gaps are. Some vehicles fit better than others although 100 % of all projects will require some work in this area. Perfecting these problems is part of “Our Mandatory Guidelines.” As seen the gap is large at the top and small at the bottom, the body point lines do not match and the moldings separating the green from the black do not line up either.

Another common example of bad factory fit is the pot metal or die-cast extensions found on most 1960 through early 70s vehicles. As seen the trunk to qter gap is large but the trunk to qter extension above the taillight almost hits.
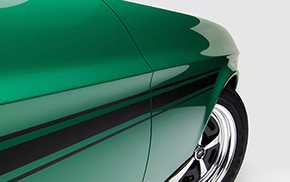
The end result speaks for itself with a flush panel-to-panel fit that no man could criticize. We have formulated many systems in the last 50-plus years to give your special vehicle the edge when the ultimate finished product is seen.
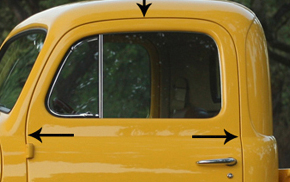
This is the goal, consistent, level panel fitting with even gaps all the way around the door. As stated you have to have the expertise to achieve this look. Proper weather strip tension, cutting back the edges then welding them with out warping, rebuilding and upgrading the door hinges, tweaking the door catches and strikers, micro grinding of all welds to keep from removing the base metal and having the eye to file all these gaps to this consistent level are just a few of the necessary techniques needed.
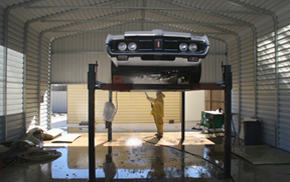
After our initial inspection we pressure wash all outer body panels including the bottom side floor and engine bay to inspect for rust and to remove oil and grease that may cover up factory markings on original builds. Our dis-assembly shop features a 4 post lift with extra ceiling room to accomplish this phase efficiently.
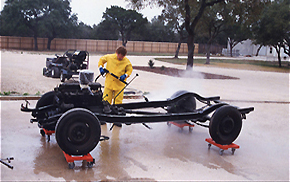
If your project is a full framed vehicle the same procedure is performed. They are done separately as the body and frame together can cover up some of the floor.
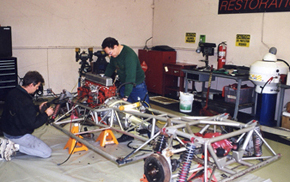
We begin the disassembly and photograph all the parts during removal. Classic car manuals are very helpful but they do not show the location of every part. We also note the best order or sequence of how a part is attached in comparison to other parts in the same area of which the shop manuals often over look. This helps the reassembly run smoother.
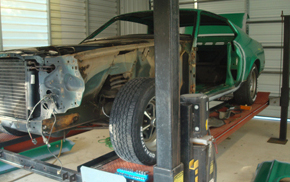
Our 4 post lift aides in removing parts from the underside, top side and also helps the photographs be taken at eye level.
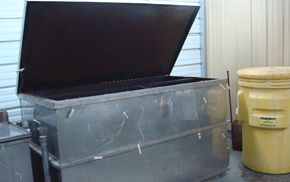
During dis-assembly most of the parts removed are dirty and or greasy, we separate the good parts from the ones to be replaced and then they are Hot Tank cleaned automatically while we stay working on your project. Note the rolled up tags which keep track of all the parts. We have separate tanks for grease removal, paint removal and rust removal.
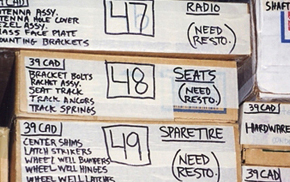
All parts to be restored and refinished are then cataloged and stored numerically. See our Mechanical shop tour for more info.
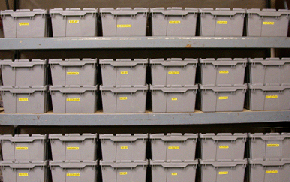
Various shop classic car manuals and the photographic history are kept in separate bins for each project. The mobile bins enable us to bring the technical info we have collected to the project if need be.
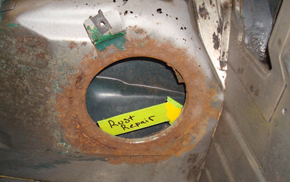
At this point we remove all the undercoat and inspect for rust damage in order to decide if we will purchase new metal, or have to fabricate areas like this drain well, of which is not mad
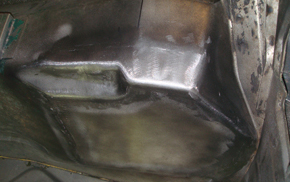
Many shapes and contours are in this piece and in order to keep water from entering in to the car and causing rust out in the future it must be done perfect. As seen we sealed off the original hole or opening to help in the cause. With A/C installed the customer sees no reason to let outside air in to the car.
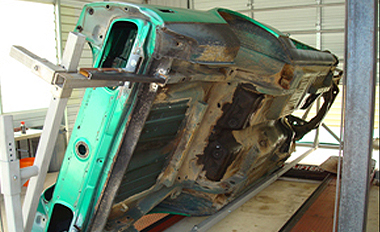
The next step is to put the body and frame on a rotator to enable easy access during removal of all the undercoat from the body. We also strip the paint down to the bare metal. If there are previous repairs with old filler such as lead, bondo etc we remove these to get to the root of the problems. More often then not the old repairs were filled over and require metal work to remove the dents correctly.
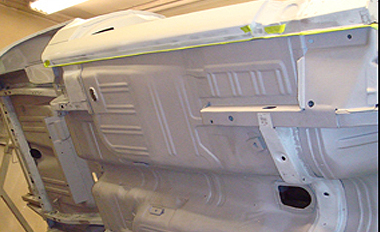
Our indoor blasting shop enables us to media blast 365 days per year to a white metal clean surface. We do an initial blast to detect all the pin holes. We then inspect and repair all metal rust out and dents before a final blast. Then epoxy primer is applied.
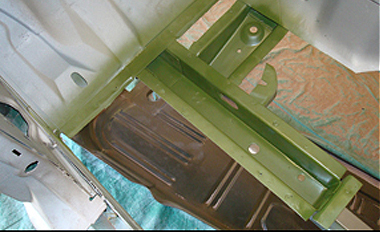
As seen we had extensive floor work to perform. We zinc chromate inside all frame structures for added protection. We do not believe in complete acid dipping of the body because the companies that offer it, rarely rinse the bodies thoroughly or long enough to remove all the chemicals that get trapped in the seams, which weeps out causing paint peel afterward. Our system is the only way to be sure you do not run in to such problems.
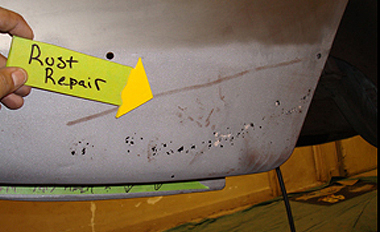
When you start to blast the pin holes come to life and are easily spotted. Depending on availability we can purchase original metal in the form of NOS or New Old Stock, solid used metal from Arizona and southern California salvage yards and occasionally reproduction if it is of good quality. Much of the time we will fabricate it ourselves from new steel or aluminum in the correct gauge especially lower body sections where moisture sits like this lower qter. 30-60 year old vehicles are usually thin or gone in these lower areas of which used metal would not be an option.
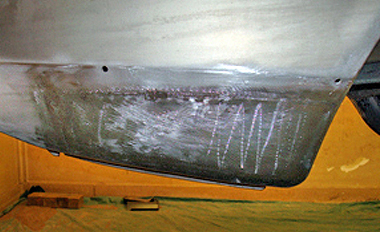
As seen just like the factory we fabricated this from scratch and it is ready for primer.
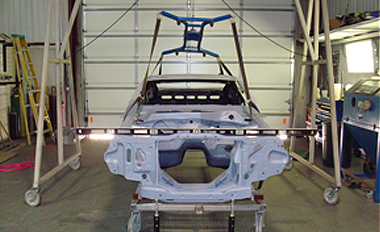
After we have primed all the metal we level out the body and start the panel alignment process. Our Mobile body dropper lowers the body down to a body Cart which is attached at the suspension points to resemble the way the car would sit with full suspension on it. This is vital for a straight, ripple free body once painted.
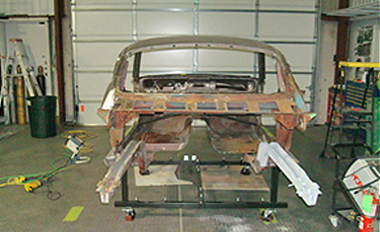
If the project comes in for a re-body we will approach it a bit different. As seen the customer brought us in a 66 Fast back Mustang with just a roof, fire wall and some frame rails sticking out the back.
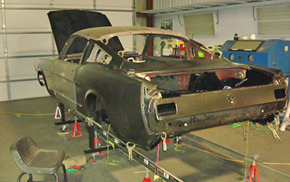
Our experts have this Stang re bodied and looking good. A combination of original and hand picked reproduction steel was used to build this car.
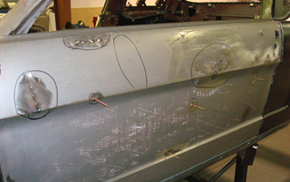
Dents are removed from the body using various tools, here a stud gun was used and after the pulls are made we simply cut them off and grind them away.
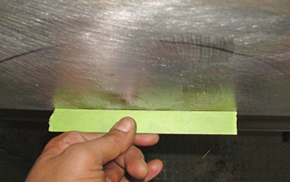
The results are nice with complete removal of the small dents.
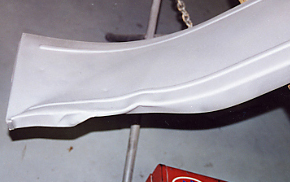
When we encounter large dents and or smashed parts many of them are irreplaceable and have to be straightened such as this all steel 1928 INT Fender. To accomplish this correctly you have to have old school knowledge as these techniques can only be performed by a few individuals with these talents.
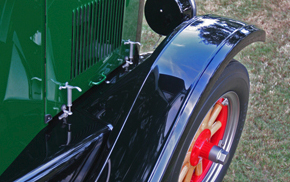
Needless to say the result speaks for itself on this finished Truck fender.
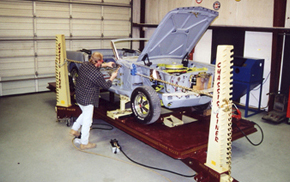
At this stage of the build we would also assess if any pulls were needed to the body or frame and make those adjustments.
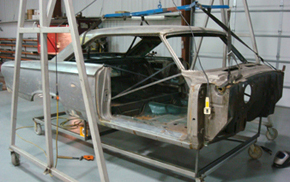
On Hot Rods we often build new frames and a decision would need to be made if the floor system would be cut out and re fabricated or to use the original floor. Clearances, cleanliness and design all add to the decision making.
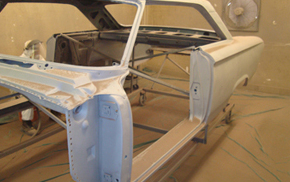
On this particular project a new floor will be built to accommodate a new frame so after floor removal we blasted all the attaching points for clean welds to our new floor. Many cars have the body panels altered for a custom looking vehicle and those decisions would be made at this time.
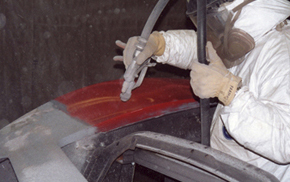
Fiberglass cars and parts are blasted using plastic " barrel" media to remove all the paint while protecting the base materials. See our Corvette section in our finished work gallery to see some beautiful VETTES.
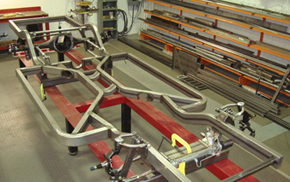
We can build a chassis from scratch and or purchase a new one from various MFG's. We can also tweak or alter your original frame to compliment your project. Depending on the popularity of your vehicle there may or may not be a full frame that is pre made to bolt to your body. Either way will help the handling, braking and overall performance. Time to set the body down for her maiden fit to determine our flooring system and other mods.
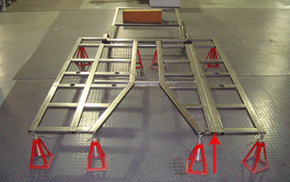
During the fabrication process of a custom hot rod many factors are considered including the hiding of wires and lines inside the tubing rails for a cleaner look. As seen at the "RED" arrow we will run wiring and fuel lines inside those tubes.
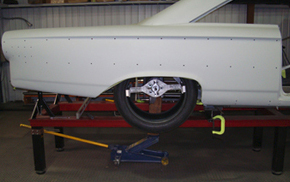
After the body has been sat in place one of the first things we do is to fit the project for tires and wheels to determine the ride height and get the "look" we are after.
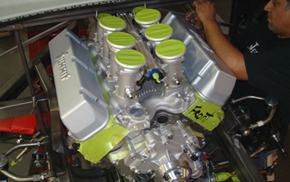
Next we fit the engine and trans along with other components to make decisions on the overall build.
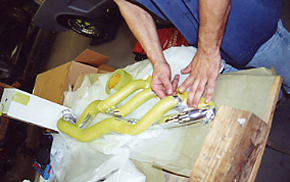
All polished parts get taped for protection during fit and fabrication. Hot Rods are approached differently then a restoration project. See our fabrication page for a few samples of custom parts we are capable of.
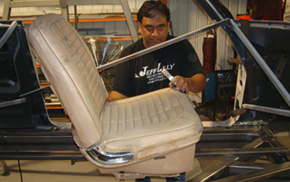
The seating comfort is custom fitted to your body as we take in to consideration your weight, height and reach when building a custom vehicle. Making sure your steering wheel, gas, brake and clutch pedals are positioned for ease of use makes a big difference on a 20 minute or longer drive. We take all factors in to consideration when performing the art of Hot Rod building. Once all the fabrication is completed we go on to the next phase.
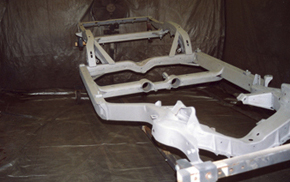
Frames original or custom are then blasted with 80 grit aluminium oxide then primed and sanded before paint.
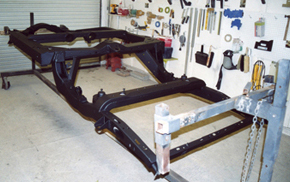
Once primed we wrap them like a mummy to protect them from dust. We then re-attach the body to the frame while we work the bodies to keep them properly supported during the block sanding phase.
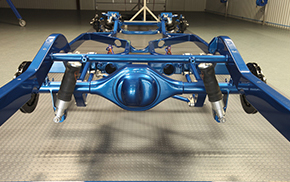
Once the frames are painted they are assembled and ready to install the body. As seen this Galaxie frame is looking good.
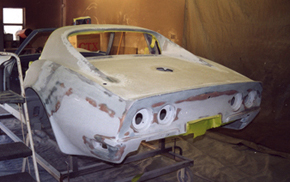
Body work is performed to smooth the panels for that super straight appearance. This includes fiberglass repairs on Corvettes and Shelby Mustangs. Aluminum bodied vehicles and of course steel bodies.
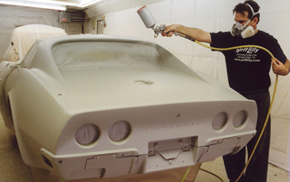
The most inspected area is the body and paint on your Classic. The body/block sanding is a vital part of the process. In addition curing is extremely important and must take place between rounds of blocking and priming. All primers have to cure as they shrink back with time and if they are not given time to sit and cure you will see waves and ripples in your finish 6 months down the road after painting which we will not allow. Texas is the perfect place for this procedure. We roll your car or truck body outside on to our curing pad each morning while staying busy working on other parts of your project.
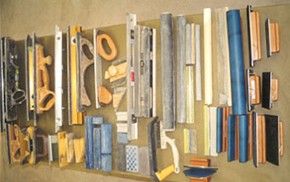
We have custom built many sanding blocks to perfect any shape your body style can challenge us with. Including double wide, single, thin, flex, contoured etc.
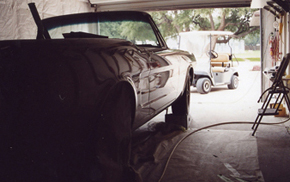
Each car is wet down to inspect and mark for any ripples. We then work them out before any paint is applied to ensure the straightest bodies in the show car business.
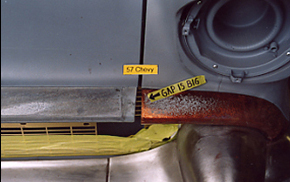
Another specialty we do during the body blocking phase is to fit and correct problems with all the trim including chrome plated pot metal parts and bumpers along with stainless and aluminum trim. As seen we have a big factory flawed gap between the hood and fender extension. Combining specialized techniques with welding rods that are plateable we can close up the gaps and make them fit as well as the body panels.
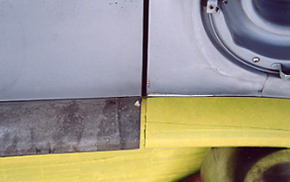
As seen we have this fitting good and are ready for the copper plating phase. See our "build tips" page for more information on this subject.
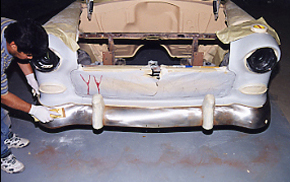
The steel bumpers are fitted, dents removed, filed, power sanded then hand sanded to accept copper. The copper is then sanded and polished before the nickel and chrome is applied. Hand worked is the only way to the city of "Perfection" and our group of talented builders only know one way, MAXIMUM!
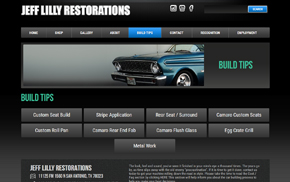
A copy of our build tips page shows a select few of our specialized techniques. Check it out when you have some time.
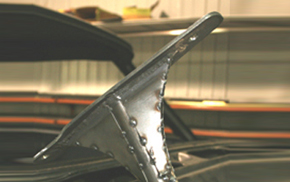
A close up of a custom hood hinge shows a nice subtle style and is ready for smoothing and paint.
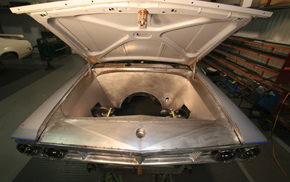
Auto lift hood using hidden hydraulic cylinders is a nice touch.
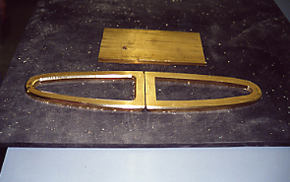
Chrome trim NOSTRILS on a 50 Ford truck custom designed from Brass stock. Then filed, sanded and copper plated before nickel and chrome.
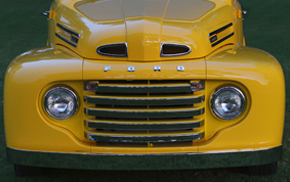
The new nostrils look great on this custom truck.
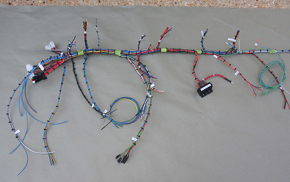
When building custom vehicles complete wiring systems have to be built to control all the upgrades added. See the "Build Tips" page for more details.
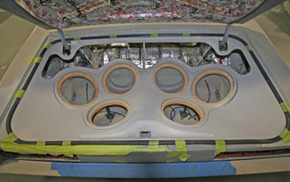
We build both high visible sound systems and hidden systems that sound great but are undetectable from the human eye.
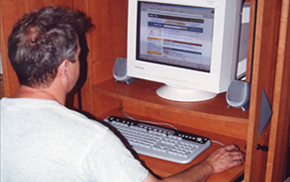
During the build of an original or custom vehicle many parts will have to be located. Our hi-speed internet computers help our efficiency in finding any and all parts at the best prices of which are passed on to you at no profit to us. All original invoices are sent to you for reassurance.
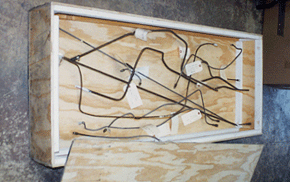
Some parts will have to be shipped and when this is needed we have special boxes to keep the rough shippers from damaging rare parts.
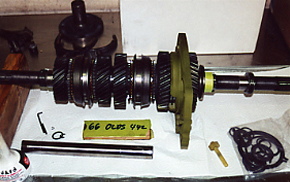
Mechanical rebuilding is also done during this time like this 66 442 4 speed trans.
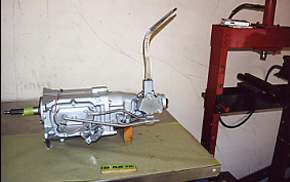
Completed and detailed trans is finished see our mechanical shop for more details.
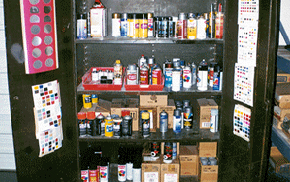
The mechanics have to detail numerous parts and an array of silvers, blacks, grays and clear coats are needed to make it happen. " Details make the Difference."
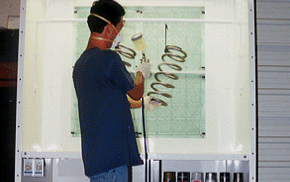
Our mechanics paint booth handles all the chores of the small parts with an infrared heater to cure the paints efficiently.
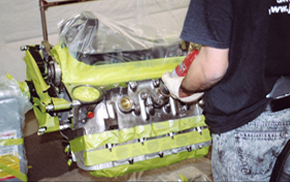
Prepping the engine to a shiny cast iron proves the cleanliness level and this is the only way to achieve long lasting adhesion on this type of metal that is subject to high heat. " There simply is no other way "
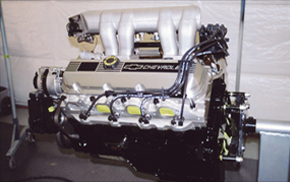
We use high heat clears on aluminum heads and intakes for Max longevity.
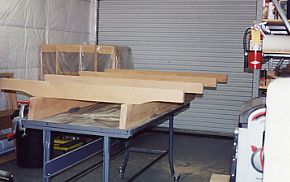
Wood work is another one of our in house specialties, here a wood bed is being built from scratch for a 1928 INT. We also build custom wood for Hot Rods.
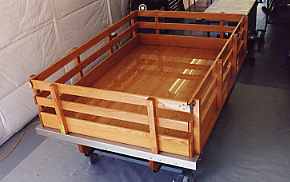
he finished piece is a sight to behold and doing everything in house keeps our quality at the highest level year round.
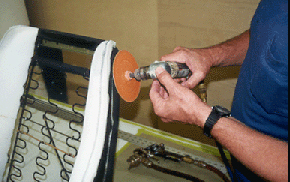
Our in house upholstery shop can handle any challenge from stock to custom built interiors.
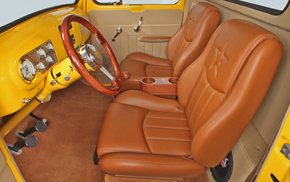
The finished work shows great detail and beautiful french seams. Once again all done in house to control the quality.
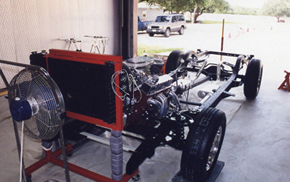
Once a chassis is done we install the drive train, then pre run as a unit to tune before installing the body .
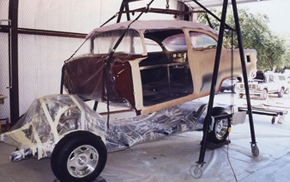
As seen we have the pre finished frame and drive train wrapped like a Mummy to preserve and protect during the paint stage. The bodies are then dropped on to the frame and final blocked. We do not paint the bodies on a rotator or cart because they could move some once put back down on to the frame. This means you would have ripples in your side panels caused by settling and flexing. There is only one way to build a project and that is how we do it to succeed in the quality and longevity of your vehicle.
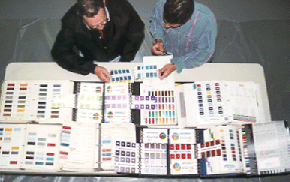
After deciding on the color with the customer we mix up German paint by Glasurit or BASF and get ready to spray.
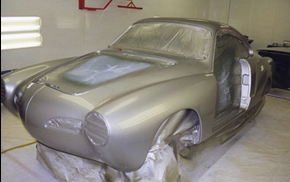
The paint booth gets her turn as we apply base coat, clear coat and or sometimes straight line paint depending on the application.
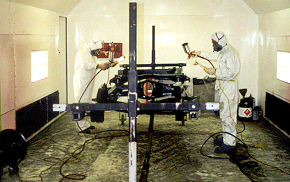
Often we will tag team spray to achieve Max results especially on frames where there are so many inside and outside areas to cover. Working as a team to paint a frame brings the highest quality.
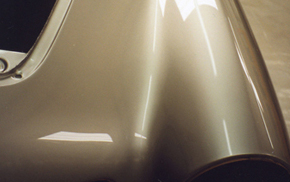
Once we color sand with 1000, 1200, 1500 and then 2000 grit paper we polish to a finish like this. Does the word "Mirror" come to mind? See our finished work on our Gallery page for some incredible pictures that showcase our " Top Level" paint work.
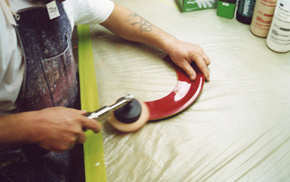
Small parts require the same love and we have the small buffers to get the results.
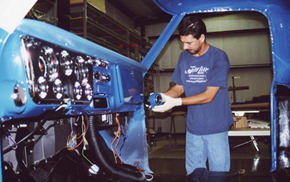
After all the polishing is done we assemble the vehicles carefully using latex gloves to avoid scratches. In addition the gloves keep the acidic moisture of human hands from tarnishing any parts.
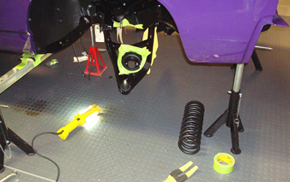
Assembly continues until they are done.
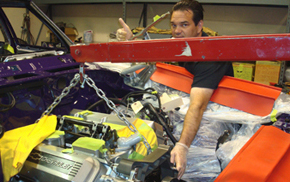
Jeff is a working manager and oversees all work.
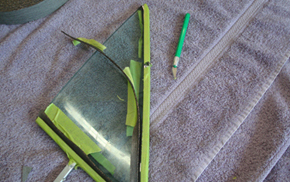
We do it all including glass installation.
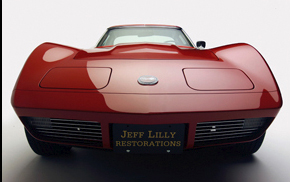
The finished work says it all. Look at the fit of the panels and the depth of that paint. Quality rarely seen!
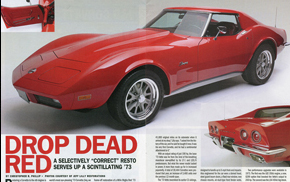
We have many connections for magazine coverage of our customers projects and we offer studio photography packages. This is a major plus when national coverage is desired.
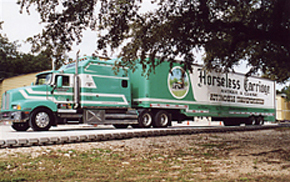
After our test drive we coordinate the transport services to our customers location.
Jeff Lilly Restorations
FAQs: Build Process
What is the custom car build process?
The custom car build process involves disassembling a vehicle, meticulously inspecting each part, and rebuilding it with modifications tailored to the client's dream car. This comprehensive process includes body panel alignment, rust removal, media blasting, custom fabrication, and engine work. The goal is to create a street-legal custom build that automotive enthusiasts can showcase at car shows.
How do you document the custom car build process?
We document the custom car build process extensively through photography and detailed records. We typically take 200-400 photos during disassembly and 2000 plus photos throughout the build. We also keep records of all phone calls, original receipts, and build plans. This thorough documentation ensures transparency and peace of mind, showing the true condition and progress of the vehicle.
What are the initial steps in building a custom car?
The initial steps in building a custom car include a thorough inspection of the base car, pressure washing to remove dirt and grease, and disassembling parts for a detailed examination. This helps identify issues with body panels, gaps, and rust, and sets the foundation for the custom build.
How do you ensure body panels fit perfectly?
Ensuring perfect body panel fit involves various techniques, such as adjusting weather strip tension, welding without warping, rebuilding door hinges, and micro-grinding welds. This meticulous work ensures consistent, level panel fitting, which is crucial for the vehicle's aesthetic appeal and structural integrity.
What is the role of media blasting in the custom car build process?
Media blasting is essential for removing paint and rust, exposing any underlying issues such as pinholes. It provides a clean, white metal surface for further inspection and repair. This step is vital for achieving a high-quality finish and ensuring the longevity of the vehicle.
How do you handle rust removal during a custom car build?
Rust removal is performed through media blasting, zinc chromate application, and fabricating new metal pieces when necessary. We inspect for pinholes and use high-quality materials to ensure the rust removal is thorough and long-lasting, maintaining the structural integrity of the vehicle.
What types of custom fabrication are involved in car building?
Custom fabrication includes creating new frames, altering body panels, and building parts from scratch using new steel or aluminum. This can also involve hiding wires and lines for a cleaner look and custom fitting for tires, wheels, and engines. Each custom build is tailored to meet the specific needs and preferences of the client.
How do you manage the restoration of classic car parts?
Restoration involves cataloging and storing parts, cleaning them in separate tanks for grease, paint, and rust removal, and refurbishing them with techniques such as welding, grinding, and polishing. We ensure that all parts, whether original or aftermarket, are restored to their optimal condition to work seamlessly in the custom build.
What is the importance of panel alignment in custom car building?
Panel alignment is critical for achieving a flush, ripple-free body. It involves using specialized tools and techniques to align panels and ensure even gaps. Proper panel alignment is essential for both the aesthetic appeal and structural integrity of the custom build, ensuring the vehicle looks and performs at its best.
How do you address imperfections in body panels and trim?
Imperfections are addressed by using specialized techniques such as stud guns for dent removal, welding rods for gap adjustments, and detailed sanding and polishing. This ensures that all parts fit seamlessly and contribute to the overall quality and appearance of the vehicle.
What materials do you use for custom fabrication?
We use high-quality materials such as new steel, aluminum, NOS (New Old Stock), and reproduction parts when available. For fiberglass parts, we use plastic media blasting to protect the base materials. Using the best materials ensures the durability and performance of the custom build.
How do you achieve a high-quality paint finish?
Achieving a high-quality paint finish involves multiple steps, including epoxy priming, meticulous block sanding, curing primers, and using high-end paints like Glasurit or BASF. We employ tag team spraying and color sanding for the best results, ensuring the vehicle has a mirror-like finish.
What is the process for rebuilding the vehicle's mechanical systems?
Rebuilding the vehicle's mechanical systems includes detailing parts, using high heat clears for aluminum components, and ensuring all mechanical parts are restored to their original or enhanced condition. This step is vital for the vehicle's performance and longevity, ensuring it meets or exceeds street-legal requirements.
How do you ensure the interior matches the custom build quality?
Our in-house upholstery shop handles all upholstery work, ensuring custom-built interiors with attention to detail. This includes creating comfortable seating positions, custom woodwork, and high-quality finishes that align with the overall aesthetic and functionality of the custom build.
What happens after the custom car build is completed?
After completion, we conduct a thorough test drive to ensure the vehicle performs flawlessly. We provide studio photography for magazine coverage if desired and coordinate transport services to deliver the vehicle to the customer's location. This ensures the entire process is seamless, professional, and meets the client's expectations.
How do you incorporate new ideas and latest technology into custom car builds?
We incorporate new ideas and the latest technology into custom car builds by staying informed about industry trends and advancements. This includes using modern tools and techniques, high-performance aftermarket parts, and innovative design elements to enhance the vehicle's performance and aesthetics.
How do you manage the budget and cost of a custom car build?
Managing the budget and cost of a custom car build involves detailed planning and transparent communication with the client. We provide cost-effective methods without compromising quality. All original invoices and receipts are shared with the client to ensure transparency.
What are the stages of the custom car build process?
The custom car build process includes several stages: initial inspection and disassembly, rust removal and media blasting, custom fabrication and body work, mechanical system rebuilding, interior customization, painting and finishing, final assembly, and testing. Each stage is critical to achieving a high-quality, seamless build.
What types of vehicles do you specialize in for custom builds?
We specialize in custom builds for a wide range of vehicles, including classic cars, hot rods, race cars, and custom vehicles. Our expertise covers various models and makes, allowing us to create unique, high-performance vehicles that meet the specific desires and requirements of our clients. 1932 to 1973 vehicles are what we specialize in.