Build Tips
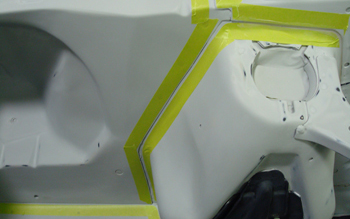
Just before paint you will need to caulk the seams on your projects body. Any visible seams should be done to give a smoother appearance and keep water and rust stains from appearing. Apply 3/4 masking tape on the lap side or higher edge about 1/16th from the drop off edge. On the over lapped portion or lower side move the tape back 1/8th to3/16th of an inch. Using 3M 8300 sealer cut the tip to allow a 1/8th bead. This product can be finger stroked with lacquer thinner to make it extra slick, peel the tape away after 1 foot at a time is finished. After one hour you can prime/paint over it.
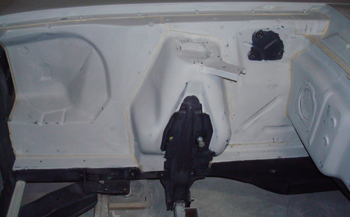
As seen the seams are all sealed providing a very smooth transition from each panel. Once all is sprayed and assembled it will look great.
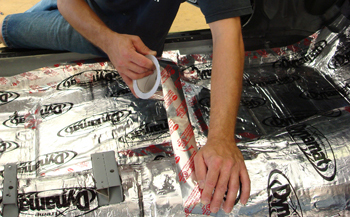
When installing dynamat to sound deaden your ride place aluminum tape on all the overlaps. This will keep the sticky black butyl from getting on your clothing/skin while working inside the vehicle especially if it will be several weeks before the carpet is installed.
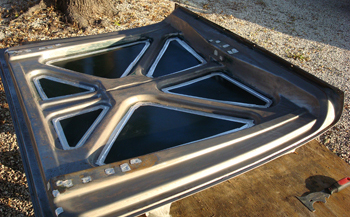
During paint stripping use aluminum foil tape to seal off the inner panel from the outer. This will keep the old paint and stripper from entering in to the inner structure and becoming trapped causing a big problem later on during refinishing. In addition place it over any holes. Simply take a scotch brite disc on an angle grinder to clean all the paint off the edges down to the bare metal where the tape covered it to finish the process.
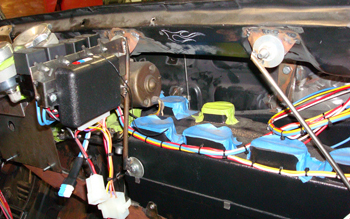
When mocking up components such as this A/C box cover the inlets and outlets with tape to keep dust and grinding grit from entering the chamber. It is very difficult to remove all debris once it gets in to such parts.

Simple things like left over exhaust tubing with various bends/radius will provide the proper exit in the best direction on Heater Boxes and A/C ducts when trying to run through tight areas up under the dash. TURN
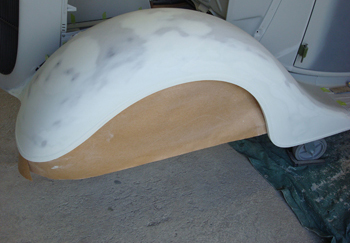
As seen on this body worked fender, masking paper was taped behind it. This not only provides cleanliness during priming but allows you to see how perfect your wheel opening is when standing back 5 10 feet. It eliminates your eyes from trying to focus on too many areas at once for the ultimate inspection.
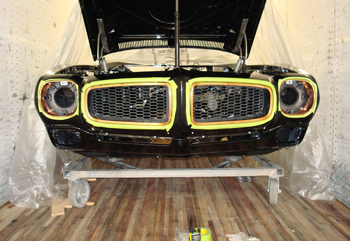
It is best to fit all the metal trim in its copper state before final nickel and chrome is done. This is the last time you will be able to correct any fit problems. Most platers over grind and tend to tweak the parts a bit during preparation and being they do not have the car in front of them to check the fit you can correct any areas you are not happy with at this time.
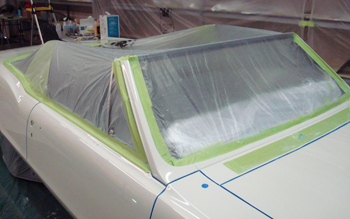
During final polishing mask the entire car with plastic and tape all the gaps to avoid polishing compounds from entering in and under trim gaps etc.
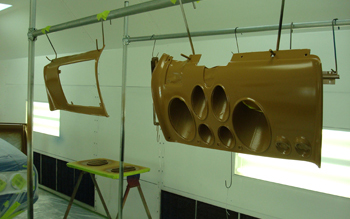
When painting small parts we recommend using 1/8th to 1/4 inch hooks to stabilize the parts. Notice the hooks are taped at the top of the rack as this keeps them from swaying during the force of air from the spray gun allowing a smooth paint job.
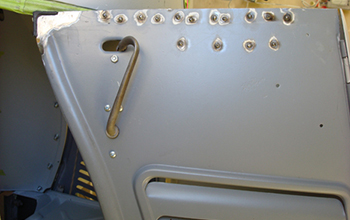
Often the edge of a panel will be wavy or unstable compared to the center especially on open panels that are not folded back. The use of a mig welder to spot a few areas and then cool with a wet rag will stiffen the panel just enough. Simply grind them back down slowly to the surface before body work and priming.
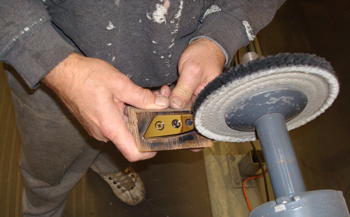
When buffing small and or larger stainless trim parts use various sizes of wood to bolt or screw them down to eliminate holding the actual part and tweaking it during the natural heat build that occurs.
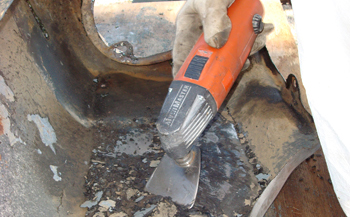
Fein built the first known power tool in the late 1800's and they are still at it today. This osculating tool with scraper attachment removes old undercoat off easily. Save your palms from carpal tunnel.
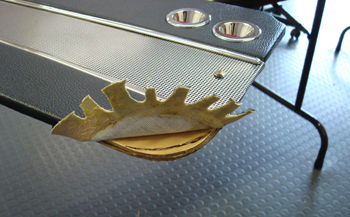
When installing factory parts such as this interior door panel they will more then likely not fit well. Hold the panel up to your door and simply mark the panel where it needs trimming then pull back the material from around the back side and trim off the excess. Then rewrap and glue for a custom fit door panel.

On older vehicles where you want to upgrade the A/C system but retain stock dash controls attach the new electronic actuators by fabricating a bracket and change the arm out to accept the original cable system.
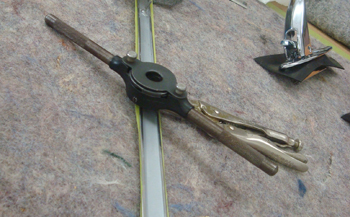
Some trim such as this Stainless Steel molding came with pot metal studs that accepted thread cutting nuts, which often slip when tightened. Using the proper thread cutting die you can change them over in to a regular threaded nut to avoid snapping off the studs during assembly if they were too tight and also avoid a loose molding when the thread cutting nuts have already cut too many grooves on the stud.
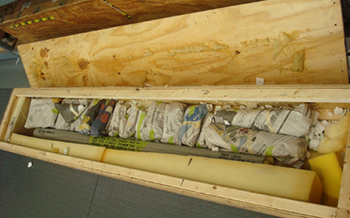
During shipping of rare parts always use wooded crates with foam and peanuts to keep them safe. I am not going to insinuate or call any one by name but those people wearing brown shorts can ruin irreplaceable parts so be extra cautious and spend the money to transport right.
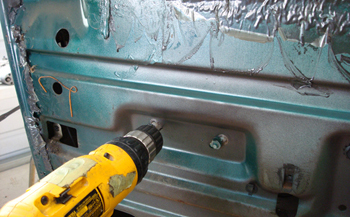
Once you have your side window glass fitting the way you like during initial dissemble or during the body work phase always pilot drill the inside doors and qters panels to the window tracks with a 1/8th bit for easy alignment during final assembly.
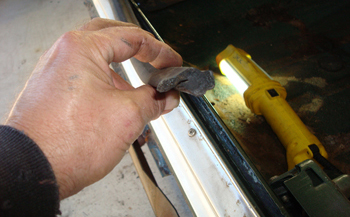
During disassembly make a note on how the factory rubber seals were put on with the profile as seen. Many shop manuals do not show you this and it can mess up the fit of your doors and deck lid if incorrect.
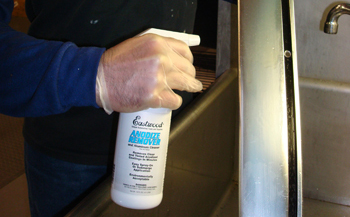
East wood has an anodize remover for aluminum parts and fittings. No need to have them sent out any more. It works good when you keep it soaked.
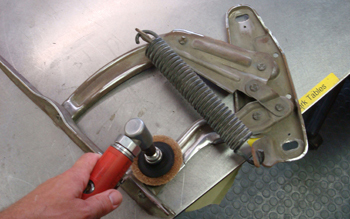
When it is time to prep our hood springs we use 80-120 grit scotch brite discs to take out small dings scratches etc. We then glass bead blast them and then silver cad plate for a nice look.
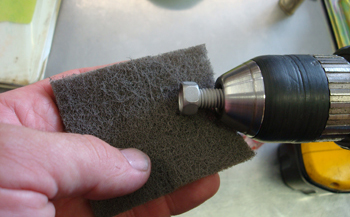
Stainless or plated bolts can have a nice satin finish on them by chucking them up in a drill and running them over a grey fine scuff pad.
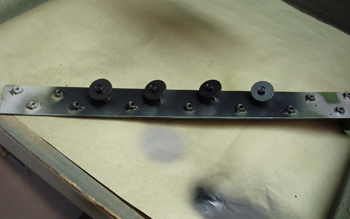
We fabbed these bolt holders to blast and paint fasteners. Simply take some 2 inch wide 1/8 thick strap material and weld different size nuts in a row. This makes an excellent holder and is an efficient process.
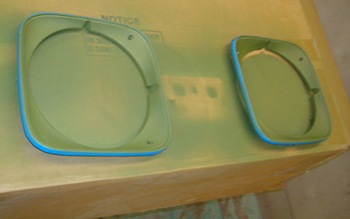
Blue fine line tape is very flexible and makes a great masking tape on chrome trim parts with concave and convex curves during painting.
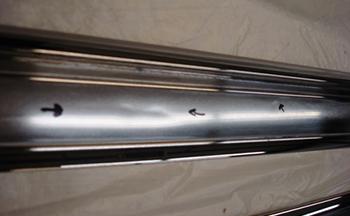
On this two step tip we have polished the outer edges on these moldings as is called for and the centers now need painting. Some body work will need to be done before painting because neither glossy nor satin paints will cover over these dings, so repairs are needed.
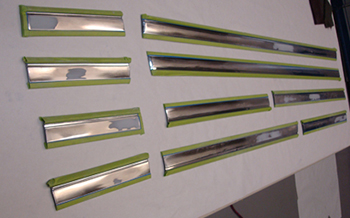
We simply used slick sand primer by Evercoat and brushed the spots. We then let it dry 45 minutes and block sanded all the ripples out. As seen we have them masked off and they are now ready to paint. We will use Ditzlers epoxy primer for adhesion on these stainless pieces then whatever top coat can be applied.
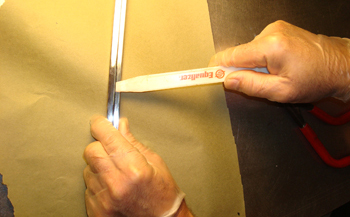
When tweaking moldings always use a wide blade plastic stick or spreader. Metal tools will damage them.
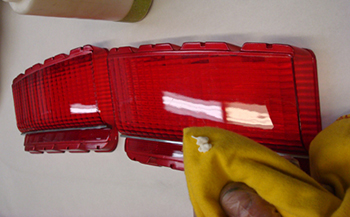
Using Finesse by 3M works great on tail light plastic to remove scratches etc.
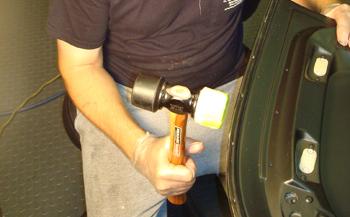
The right tool for the job is important. Jack uses a rubber hammer at 60 durometer which gives just enough, to keep from damaging small trim yet it is hard enough, to drive it on. When choosing the correct rubber mallet always remember "Durometer" this stands for the hardness of the rubber.
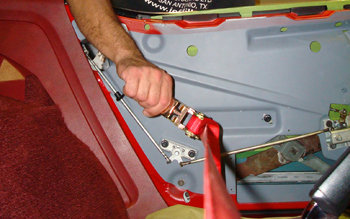
E rockin O adjust a small binder strap between the doors a bit. This is how we break in the rubber seals at final assembly. This is important if you do not want to tweak the doors outer panel causing potential ripples. We usually install some J-Hooks to the door by drilling a small 1/4 ich hole at the bottom or top of the door depending on where the rubber is the tightest and then hook the binder to them. Just a notch more every two to three days will do the trick. Remove the striker before doing this for no restriction. Once the doors close easily on their own re-install the striker.
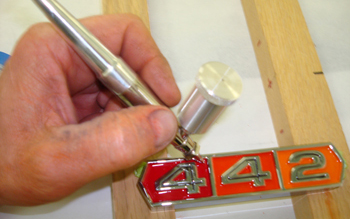
A flow pencil works great when painting emblems in between the lines
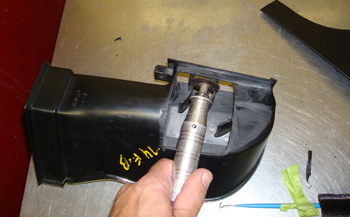
This 3 part tip shows how to adjust heater plenums and air vents. As seen Eric has cut away a section of the plenum that was hitting on an upgraded speaker system under the dash.
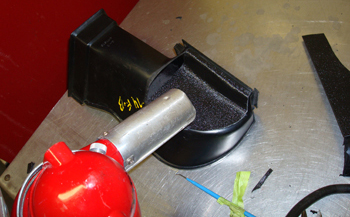
Next he takes a piece of ABS cut to fit then uses a heat gun and molds it in to shape.
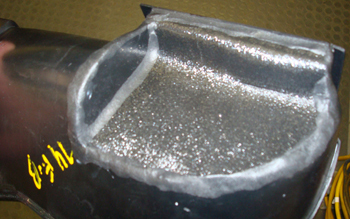
The ABS adheres well and forms around the old box giving it clearance while allowing air flow to the defroster.
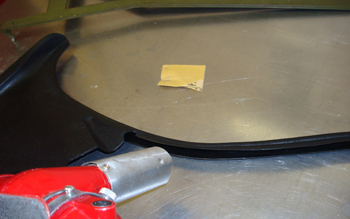
Most plastic on a car or trucks body can be heated with a heat gun to manipulate and reshape. This kick panel wind lace was curved too much from the factory so a little tweaking was needed. Heat and place it within 30 seconds, then hold it in place while it cools and you have a nice fit.
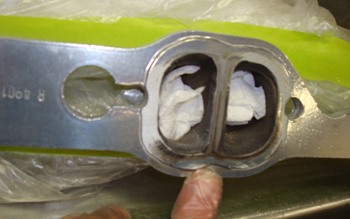
When you purchase a set of headers check them with a straight edge first to see if they are plane then make the corrections before coating and installation. As seen on this set we had to weld on the lower bead then file to a level state so it would seal. Sometimes they will be level as far as the surface goes but the factory sealing bead is either too low or too high in correlation to the gaskets. Gasket MFG's will also be different so always check the gasket to see if it matches the header.
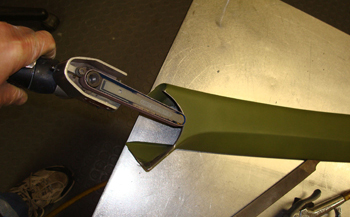
Just above the dash pad on each corner the side trim usually does not fit the dash very well. Eric marked it and using a mini file belt sander he is grinding away the unwanted metal to fit exact.
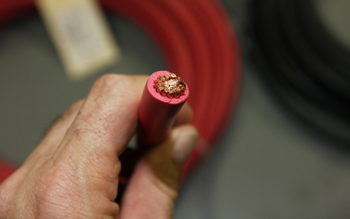
With Copper prices going through the roof be selective when choosing large cable for battery and stereo leads as many MFGs are putting extra thick plastic coatings on the outside to make the cable on the outside appear correct but the copper is 1-2 sizes too small to get the job done. Ask for a sample, or if the cable is gauged to the correct size before purchasing.